Aluminum Spreading Proficiency: Techniques and Devices for Exceptional Outcomes
Understanding the art of light weight aluminum casting calls for a delicate equilibrium of precision, strategy, and the use of specialized devices. From the first stages of thawing the light weight aluminum to the detailed process of mold and mildew preparation and pouring, each action plays an important role in attaining extraordinary results. As we check out the detailed techniques and tools associated with light weight aluminum spreading mastery, one can not overlook the value of sophisticated putting and cooling techniques that can raise the final end result. Keep tuned to reveal the important devices and completing touches that lead the way for impeccable aluminum spreadings.
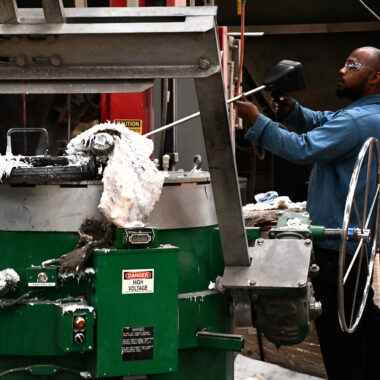
Significance of Correct Melting Techniques
Using exact temperature level control throughout the melting process is paramount in guaranteeing the quality and honesty of aluminum castings. The melting of light weight aluminum is an important action in the casting procedure, as it directly affects the last properties of the casted parts. Appropriate melting methods are necessary to achieve the preferred metallurgical framework, mechanical residential or commercial properties, and surface coating of the aluminum parts.

In addition, tracking and changing the thaw temperature level during the procedure assistance stop getting too hot, which can create grain growth and influence the general top quality of the aluminum spreading. Sticking to exact melting methods not just boosts the quality of the end product but additionally enhances the performance and cost-effectiveness of the spreading procedure.
Vital Mold And Mildew Preparation Tips
Proper preparation of mold and mildews is a basic facet in the light weight aluminum casting process, guaranteeing the successful replication of intricate information and dimensions in the last casted components. The essential mold prep work steps begin with picking the ideal molding material, such as sand or financial investment casting products, based upon the ins and out of the component and preferred surface. Before pouring the liquified aluminum, the mold tooth cavity must be meticulously cleaned up and dried to stop issues in the casting. Additionally, using mold and mildew layers can help enhance surface finish and lengthen mold and mildew life.
Furthermore, proper gating and risering style are crucial in mold prep work to make sure audio spreadings with minimal defects like porosity and contraction. The gating system helps with the circulation of liquified metal right into the mold dental caries, while risers help prevent shrinking by giving additional liquified steel as the casting strengthens. Careful consideration of these aspects during mold preparation considerably contributes to the top quality and stability of the last light weight aluminum cast parts.
Advanced Pouring and Cooling Techniques
Carrying out innovative putting and cooling methods is critical in optimizing the light weight aluminum casting process for enhanced efficiency and high quality outcomes. Using methods such as vacuum spreading can substantially decrease porosity in the end product, leading to enhanced mechanical buildings. By evacuating the air from the mold tooth cavity before putting, the threat of gas entrapment is reduced, resulting in a denser and even more structurally sound spreading.
Additionally, employing controlled air conditioning approaches, such as water quenching or air cooling, can influence the product's microstructure and mechanical attributes (about aluminum casting). Quick air conditioning can aid achieve finer grain frameworks and improved mechanical homes, making the cast aluminum better for applications needing high stamina and toughness
On top of that, implementing directional solidification techniques, where the spreading strengthens considerably from one end to an additional, can assist minimize internal problems and boost overall component integrity. By thoroughly handling the temperature differentials during solidification, the formation of Clicking Here contraction porosity and hot tears can be reduced, causing better castings with enhanced mechanical efficiency.
Essential Devices for Light Weight Aluminum Spreading
Enhancing the performance and quality outcomes of light weight aluminum casting procedures relies greatly on the utilization of particular tools developed to optimize various elements of the spreading operation. One important tool for aluminum casting is the crucible.
One more vital tool is the mold and mildew. Molds can be made from materials like metal, plaster, or sand and are used to shape the liquified aluminum into the preferred type. about aluminum casting. Proper mold and mildew design and materials are essential for attaining exact spreading dimensions and surface area coatings
Along with crucibles and mold and mildews, a heater is a basic device for light weight aluminum spreading. Furnaces warm the metal to its melting factor, ensuring it is in a state prepared for spreading. Important for keeping consistent temperatures and making sure the light weight aluminum stays molten, heaters are readily available in numerous types, such as electric, gas, or induction heaters, each with its benefits for certain casting demands.
Finishing Touches and Quality Checks
Upon completing the spreading procedure, precise interest to completing touches and extensive quality checks is vital to ensure the honesty and accuracy of the aluminum parts - about aluminum casting. Ending up touches include the elimination of any kind of excess product, such as flash, gating systems, or harsh sides, to accomplish the desired final form and surface area high quality. This action often consists of processes like grinding, fining sand, or fired blowing up to fine-tune the appearance and appearance of the actors components
Quality checks are after that performed to verify that the elements fulfill the specific needs and criteria. These checks may entail dimensional examinations using accuracy tools like calipers or coordinate measuring equipments to guarantee accuracy. In addition, non-destructive testing approaches such as ultrasonic testing or X-ray assessment can be utilized to spot any inner defects that may jeopardize the structural honesty of the components.
Conclusion
Finally, grasping aluminum spreading techniques and making use of the right tools is vital for attaining remarkable results. Appropriate melting methods, mold prep work, pouring and cooling down approaches, in addition to completing touches and quality checks are essential action in the casting process. By complying with these actions carefully and using the ideal tools, one can ensure a successful and high-quality light weight aluminum casting manufacturing.
As we discover the elaborate strategies and devices included in light weight aluminum spreading proficiency, one can not overlook the importance of advanced pouring and click for more info cooling down approaches that can raise the final end result.Correct prep work of mold and mildews is an essential aspect in the aluminum casting procedure, ensuring the successful duplication of complex details and measurements in the final casted elements. Prior to pouring the liquified light weight aluminum, the mold and mildew tooth cavity have to be meticulously cleansed and dried out to avoid flaws in the spreading.Enhancing the effectiveness Read Full Article and top quality end results of light weight aluminum spreading processes relies heavily on the utilization of specific tools designed to optimize numerous elements of the spreading operation.In enhancement to molds and crucibles, a heating system is an essential device for light weight aluminum spreading.